WELCOME TO DIP
Technology
Casting technologies are production technologies by which parts are formed by pouring molten metal into a mold where it cools and solidifies. In order to achieve a uniform quality of materials, a homogeneous and flawless appearance, in addition to knowledge and experience, it is necessary to have modern equipment that meets high standards, both in terms of the casting process itself, and in terms of environmental protection.
In the last two years, DIP d.o.o. has modernized its production process and increased the production capacity of the foundry to approx. 1000 tons per month.
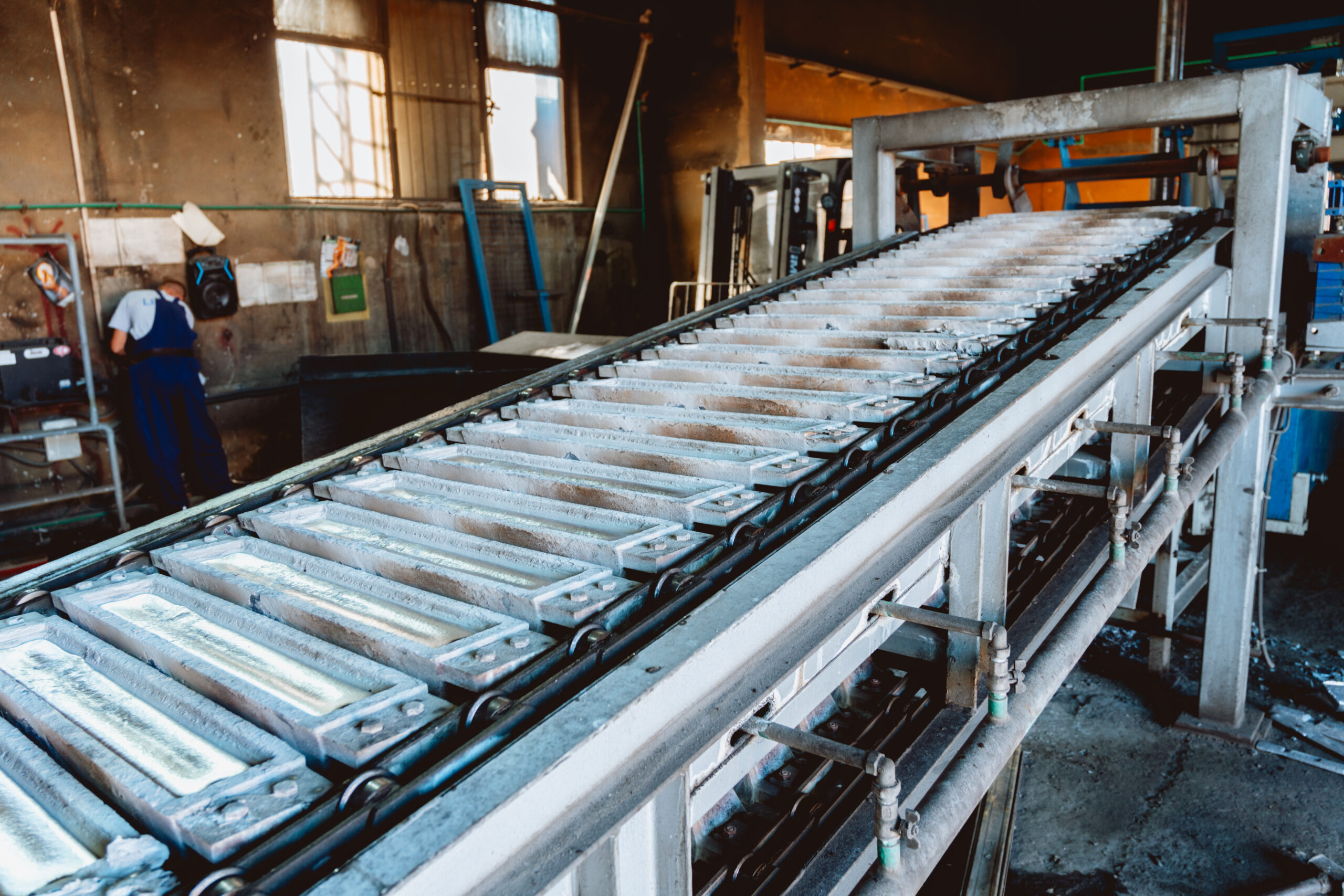
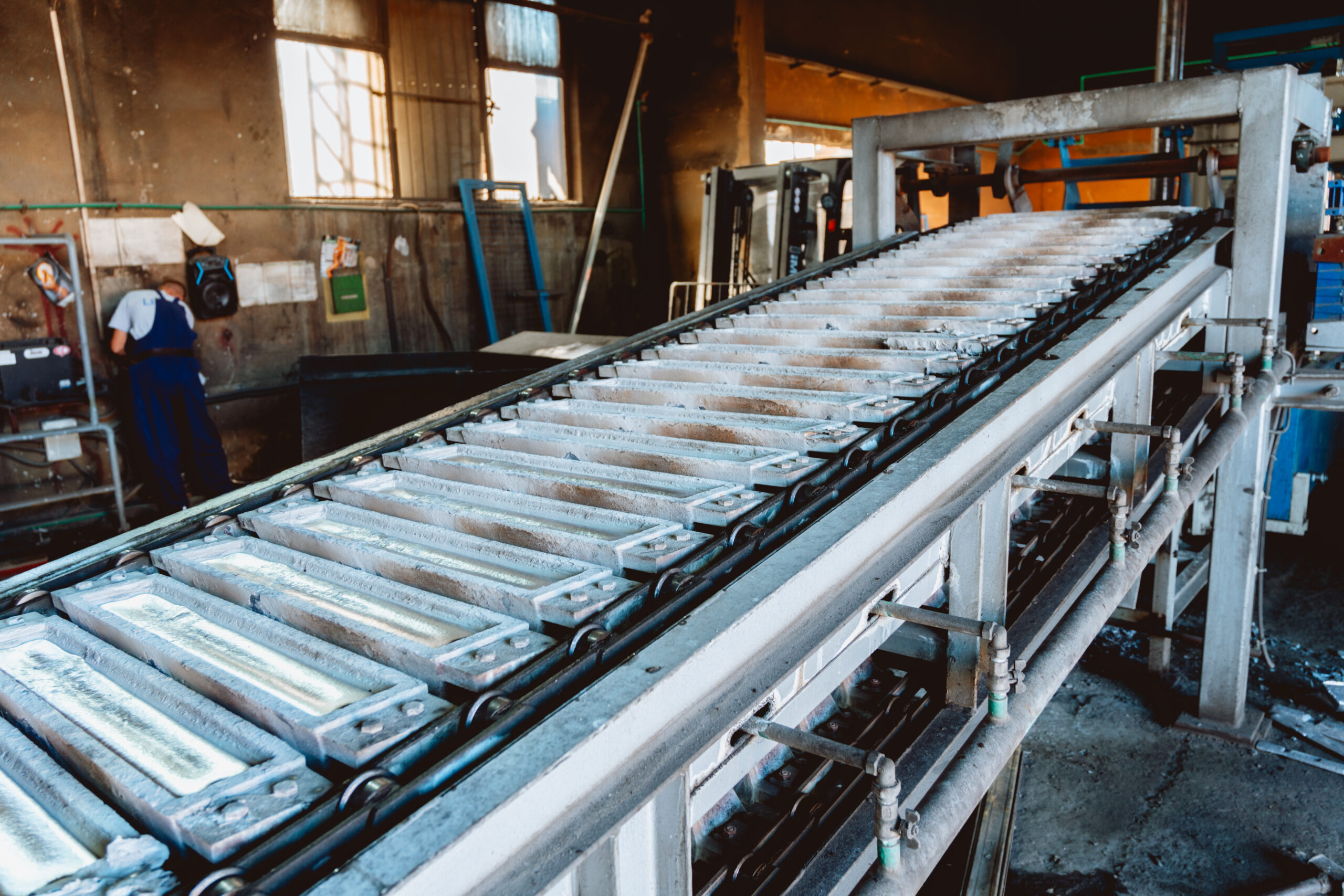
DIP Foundry has 3 furnaces:
- rotary furnace with a capacity of 5 tons/shift
- 2 chamber furnaces with a capacity of 6 tons/shift
By installing a system of bag filters for all existing furnaces, the emission of harmful substances into the air was significantly reduced and high standards of environmental protection were met.
With the introduction of automatic packaging, the work of our workers, who until recently did all the stacking manually, has become much easier, now the pallets are all same dimensions and appearance, packing is much faster and the whole process is much easier.
Diesel forklifts have been replaced by electric forklifts, both to reduce costs and to reduce noise and pollution.
By purchasing a new press, the recycling process has been significantly improved, by carefully sorting and selecting the material that is then pressed into bales, faster and more efficient filling of the furnace has been made possible.